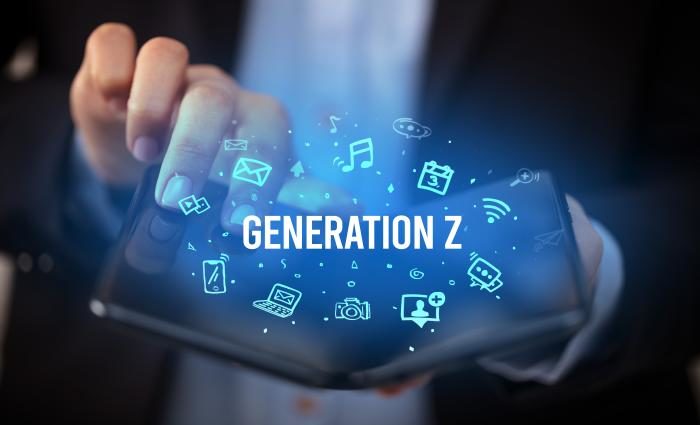
Can augmented reality attract gen Z to poultry processing?
It’s time for the poultry processing industry to get creative when it comes to hiring, training and retaining younger workers.
Poultry processing has long struggled with the issue of labor shortages – a challenge that was further exacerbated by the health and safety concerns associated with the COVID-19 global pandemic.
Whenever the issue of labor shortages come up, people always talk about automation as the solution. However, most of the promising automated technologies are still in the design phase. Is there a better way to leverage the workforce now?
Generation Z enters the labor market
The oldest members of generation Z – born between 1996 and 2010 – have begun to enter the workforce. Generation Z loves technology – which may be key to attracting them to industries like poultry processing and keeping them once they’ve started working.
“The excitement of technology for attracting new workers is a major factor,” explained Todd Gilliam, CPG Industry Manager, Rockwell Automation.
Thirty years ago, workers looked to their place of employment to connect with the latest and greatest technologies. Now, if you want to get the latest and greatest technologies, you go home.
“We have to shift in manufacturing to meet the expectation that the next generation has,” Gilliam added. “We have to be just as attractive as an employer to those constituents as competing individuals.”
Augmented reality as a training tool
The use of augmented reality to train poultry processing workers offers several benefits. The interactive, visually intensive approach to training can minimize language barriers, decrease worker errors and teach complex tasks more quickly than other methods.
It can also be helpful to younger employees that are new to the workforce.
“They grew up being comfortable receiving information and working in an augmented reality kind of environment. The reality is that printed and electronic manuals don’t work anymore,” said Steve Mulder, Americas OEM Manager, Rockwell Automation.
“When we limit time and provide just the contextualized information, I think we can really drive accuracy in these tasks, whether it’s a maintenance or an operator procedure.”
Makes sense to me. What do you think?
This content was originally published here.