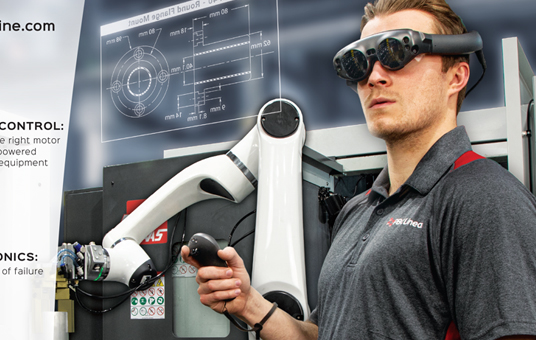
March 2022 Issue: Augmented Reality Gets Real
Motion control continues to adapt
In January, as part of our Engineering Week virtual event, our motion control editors (Lisa Eitel, Miles Budimir, and Danielle Collins) discussed with me some of the more interesting trends they are seeing, along with guest panelists Dan Zachacki of Mitsubishi Electric Automation and Nik Brightwell of Akribis Systems. I thought some of the conversation’s main points were worth repeating as we get into the groove of 2022. Here were some of the most interesting insights:
• At the OEM level, there’s demand for more sensor integration into products. Some customers want more sensing technology via analyzed performance during operation; there are some sensing technologies in the market that allow for that, but some manufacturers are having to develop their own sensing technologies. For some “dumb” components such as motors, bearings, and metal, these sensors are being integrated to make them a smarter solution — in the next two to three years we will see a much higher level of adoption.
• Engineers are discovering what features are beneficial to them in the industry 4.0 / IIoT environment, everything from tuning to predictive maintenance. Component manufacturers are incorporating these features directly into their products to make the IIoT easier to use, more user friendly, and reduce the amount of eff ort that’s required to implement solutions into individual machines. That’s going to help with the overall adoption of these concepts.
• On the purely mechanical and motion side, there’s a lot of opportunity especially for predictive maintenance to read or sense, for example, the condition of a bearing or a ball screw. But manufacturers are really struggling with how to integrate those capabilities into their products without increasing size, increasing cost, and increasing the eff ort for the end user or the integrator. Customers may like the idea of some of these benefits but may not be willing to pay for it — this is definitely a cost/benefit type balance.
• Manufacturers are doing more and more integration of both mechanical and electrical components — integrating the motor with the drive, the ball screw, the rack-and-pinion system, etc. There’s also a lot of customization that manufacturers are more willing to do now than in previous years — from the technical specifications and dimensional specifications to things like noise and footprint. These are things that make it easier for them to integrate that motion component into the end product. Manufacturers have opened up and become more willing to go that extra mile in terms of integration and customization.
• We’re seeing a general trend in motion control capabilities being added to auxiliary devices like HMIs or industrial PCs. For the most part, from the HMI perspective, they’re capable of issuing basic control commands. For more sophisticated controls like synchronized motion, these are more limited to either motion controllers or PC-based control systems that can coordinate multiple individual servo axes. We’ll start to see more of these devices integrated with motion control capabilities, but for now it mostly varies by individual manufacturers, in terms of what is possible.
• The pandemic’s supply chain issues have resulted in a shift in flexibility. A lot of engineers previously were very brand focused for some electronic components that would be integrated as part of a system. They’ve now become more flexible in looking at alternative paths — whether for encoders, sensors, or controllers. Due to these demands, people have become more able to evaluate alternative technologies.
Paul J. Heney – VP, Editorial Director
[email protected]
On Twitter @wtwh_paulheney
This content was originally published here.